Painted Aluminium Coil for Car license Plate
Signi Coat produces a range of products specifically designed for this very specialised end-use and has been a leading supplier to this market for many years, in different parts of the world.
The products include materials for embossed plates which demand extreme ductility in the base metal, as well as for the multilayer systems common in parts of Asian.
Typical license plate types:
• Pre-treated aluminium to accept retro-reflective film for subsequent embossing and overprinting.
• White coated material for embossing and overprinting.
• White coated base sheet for embossing and black coated thin gauge sheet for perforating and bonding to the base aluminium in producing a composite plate.
Material specifications
The alloy and temper requirements are related to whether the plate is to be embossed. If this is the case, the material is typically 1050 or 1200 in thicker gauges around 1.0 – 1.2 mm, temper H42
In the laminated license plate, the thinner coated aluminium is typically 3105, 0.30 mm thick.
Signi Coat ’s unique pre-treatment is used prior to the primer and topcoat paint system. The process produces a clean surface with a thin aluminium oxide film. This film is an integral part of the aluminium surface and is flexible due to its porous structure. This pre-treatment prepares the surface for excellent paint adhesion and corrosion resistance of the painted products. The pre-treatment is non-toxic and does not contain any chromium or heavy metal based chemicals and, therefore, underlines Signi Coat’s environmental friendly profile.
The coating is a special formulation with properties unique for this end-use. It must be highly flexible to withstand the drawing which takes place during plate manufacture, resistant to road salt, petrol and diesel, and yet accepts the laminated retro-reflective film with high levels of adhesion. These properties are covered in various national and international standards with which materials must comply.
The presence of a reverse coating has the benefit of assisting fabrication and reducing tool wear, due to its lubricating properties, although no lubricants are normally present. It also acts as a protector to the front coating, reducing the risk of pressure and metal marking.
Contact Form
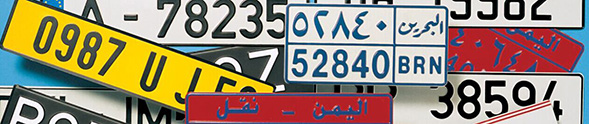